Introduction: Laser-Induced Graphene (LIG) at Home!
Hello fellow makers!
Recently in my newsfeed on YouTube an interesting video popped up where a guy created a capacitor using some kapton tape and a 405 nanometer laser.
After a reading through some research papers on the process which is called Laser-Induced Graphene my mind was racing with ideas of all of the projects that you could create at home using this simple process.
In this Instructable we will be looking at the science behind Laser-Induced Graphene and I will be showing you how to create some neat projects at home or in the classroom.
Let's get started...
Step 1: What You Will Need:
To replicate this Instructable you will need the following:
- Kapton tape
I used 10mm wide tape
- Access to either a laser engraver or 3D printer fitted with a laser module
I use this inexpensive 0.5W 405NM laser module that I mounted to my homebuilt CNC
- Microscope slides
- Painters tape
- Glass pane
- Wires
*As an Amazon Associate I receive a small percentage from sales made through provided links at no cost to you, this helps fund future projects.
Step 2: What Is Laser Induced Graphene?
Laser-induced graphene is a three-dimensional form of graphene consisting of multiple layers. Its specialty arises from its single-step, cost-effective preparation to the versatility among many carbon precursors.
The controllable fabrication, design, and texture of the material via computer-based systems hold a great promise toward printable electronics for sensing-based applications. Due to its highly conductive and mechanically robust nature, it has been applied as a catalyst for hydrogen peroxide generation and water splitting reactions.
Compared to other materials, a very low oxygen overpotential could be achieved at minimal voltage, making it an appealing tool in electrochemical applications. The inculcation of inert gases like argon or hydrogen during graphene preparation helps in tuning the surface properties of LIG from superhydrophobic to superhydrophilic.
These properties facilitate the attachment or detachment of external stimuli over the surface, which is also one of the primary reasons for its antibiofouling nature. In addition to this, LIG can be integrated with certain host materials such as metals or metal oxides, additives, or heteroatoms to form composite materials. Even embedded materials could be fabricated by transferring LIG through infiltration onto a different substrate.
Furthermore, the fascinating property of LIG lies behind it, leaving minimum to no toxic imprint on the environment, thus making it sustainable to use in the current situation.
By using an appropriate laser setting, graphene size, morphology, and texture can be easily controlled without any additional step. Lasers ranging from infrared, ultraviolet and visible ranges have been employed for the synthesis of LIG. Although LIG has been first prepared on a PI sheet via an infrared CO2 laser, later, many studies have explored the potential of different lasers, intending to improve the spatial resolution of LIG.
This method also provides an excellent platform for fabricating different graphene morphologies via variation in operational modes of laser-like pulse density, laser duty cycle, focus and defocus, etc.
You can read up more on Laser-Induced Graphene at ASC Publications
Step 3: Design:
First we will need to create a design for our graphene depending on its use.
You don't need any fancy programs to do this any drawing software will work, in fact I used Paint to create the designs above.....yes....Windows Paint!
The only requirement is that you will need to create the design with your material sizes in mind, for me this was 10mm wide and 60mm long as this was the width of the kapton tape (10mm) and the length of the microscope slides I used for the substrate (60mm).
The first design is a interdigited electrode that has one electrode on the one side and another electrode on the other side and has offshoots from either electrode that goes in between each other.
We can use this design for building either a graphene capacitor or a battery.
Next we have one that is simply a black bar almost the entire size of the tape.
This can be used as a graphene heating element.
And finally we have lines of various thicknesses.
This can be used as either a carbon resistor or a variable resistor.
Step 4: GCode:
When you have finished your design we will need to generate the gcode in order for the laser to cut it.
Now this will take some experimenting as each batch of kapton tape can differ slightly and will also depend on the laser module you are using but you can start with my settings and adjust until you get satisfactory results.
For all my laser cutting I always use LaserGRBL.
I started with 100% power which is 500mw or 0.5 watts and while it worked for the interdigited electrodes as soon as I started the heaters which are much larger areas it overheated and cut through the kapton tape.
My best results where with 80% power which is 400mw or 0.4 watts and a cutting speed of 700mm/min with a focused beam, this gave me perfect results every time.
Note that if you are cutting faster or with the beam slightly out of focus (bigger beam width for overlapping) you will need to increase the power.
Step 5: Prepping:
Now we need to get the kapton tape ready for the laser.
Take your microscope slides (you can use other materials for substrates but I found that the microscope slides work the best because they are the perfect size for testing and the kapton sticks to it perfectly flat) and wipe away any dirt or oils with a clean cloth, now apply a strip of kapton tape across the length of the slide making sure there is no air bubbles.
Next I placed a small piece of painters tape onto the corner of the slide just to make it easier to focus the laser on the top of the slide and also across a sheet of glass that I then aligned with the laser head so it will be easier later on to align the kapton tape with the laser.
TIP: As seen on the 2nd to last photo even with the laser set to the test/focusing power which is usually 1 to 5% power it is still difficult to see the actual laser spot but by holding an extra pair of of safety glasses over the lens and letting the laser shine through it, it removes the light spillage and you can easily see the focused dot.
Step 6: Making the Graphene:
WARNING!
MAKE SURE TO WEAR ALL THE NECESSARY SAFETY GEAR WHEN WORKING WITH LASERS
Now we can start making some graphene!
Place your microscope slide under the laser and align the kapton tape with the painters tape we placed onto the bottom glass pane.
Now check that your laser is focused and set it to the corner of your kapton tape and you're ready to go.
Step 7: What Can I Use It For?
Next I will be showing you three examples of what can be done with the Laser-Induced Graphene but the possibilities don't stop there, there are many MANY more fun experiments that can be done with this simple process.
Step 8: Graphene Heater:
First up we have one of my favorites the graphene heater.
Instead of sticking the kapton tape to the microscope slide I placed two layers on a piece of 0.5mm 90mmX30mm aluminium plate.
I then burned a 60mmX9mm (the same as on the glass slides) rectangle onto the kapton tape with the laser.
Next I took two pieces of wire and stripped both ends clean, I separated the wire strands and placed the two wires on either side of the graphene with some more kapton tape as pictured to create my heater for testing.
The resistance of the heater was 285 ohms.
I attached a 35 Volt power supply to it and the heater drew 130ma of current.
Starting at an ambient temperature of 55 degrees Fahrenheit the heater reached a temperature of 161 degrees Fahrenheit in under a minute and maintained a temperature of between 159-163 degrees.
Overall I'm very happy with the results of this heater from only 4.5Watts of power.
This would be great to create custom heated glass beds for 3D printers or flexible heaters as shown in the last picture.
Step 9: Variable Resistors:
Next up we have an old classic... the carbon resistor
By drawing simple lines of various widths and lengths we can create our own custom values of resistors or even a variable resistor.
I found the measured resistance to be pretty accurate depending on the widths of the lines when measuring the same lengths.
The resistance of the piece also depends on the power setting of the laser and the engraving speed.
This can be a really fun classroom project to give a list of resistances and let the kids design their own resistors to match those resistances as close as possible.
Step 10: Graphene Capacitor/Battery:
And finally we have the graphene capacitor.
Now this is one I'm still experimenting with a bit.
I started with the interdigited electrode on the kapton tape which I then added a wire to each end using some more kapton tape.
Next I placed some cotton wool over the electrodes (but I would suggest rather going with a piece of folded up tissue paper as it wicks better) and place another microscope slide over it.
I added an electrolyte which in my case was a weak lye solution to the cotton and pinched it in a clamp.
I shorted the leads out for a few minutes and then charged it up using a AA battery.
The measurements I got was 240uf capacitance at 0.4 volts.
There is still a lot of experimenting left here!
Step 11: UPDATES:
Update 1:
I did some further experiments with the size of the laser dot, by slightly increasing the size (defocusing) I could get the lines to overlap more.
Initially under the microscope the results looked promising but when I tested the strip it had a very high resistance which leads me to believe that the graphene didn't fully form.
This was due to my current laser setup (500mw 405nm module) not having enough power even when reducing the speed of the machine.
Step 12: Enjoy!
I hope you guys find this Instructable useful and if you have any questions please feel free to leave me a message or comment bellow.
Please share your own creations with us by clicking the "I Made It" button below.
Happy making!
---
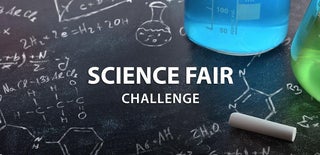
Second Prize in the
Science Fair Challenge
10 Comments
1 year ago on Step 8
What is the purpose of aluminum rather than glass on this step?
Is it for thermal conditions? space?
1 year ago
Hi I am sorry but I cannot see what is going on here. Are you burning the surface of the Kaptan tape with the laser into the pattern shown and connecting them to a battery, but the two halfs are separated from each other, so no current can flow. Also what is the piece of tape that appears to be burnt all over, is that stuck on top as a capacitor plate or is its burnt surface in contact with both side of the first plate?
regards John
Reply 1 year ago
Hi, the laser energy converts the polyimide film used as the base material of Kapton into a sort of graphene foam.
Reply 1 year ago
So where is the connection between the two comb shaped plates or is there LIG in the area that looks like virgin Kaptan between them. OR is the connection made via the sheet of Kaptan that appears to be stuck over the comb area?
Reply 1 year ago
Step 10 shows how it is constructed, on top of the comb shaped graphene I placed some cotton wool soaked in an electrolyte.
Reply 1 year ago
Understood, thank you, its just the dark strip looked like the Graphene comb.
1 year ago
Check out Broken Taps on YouTube for the video on this, he explains the process very well and goes into depth on what happens in the tests.
Question 1 year ago
what turned black? is it the adhesive on the bottom of the tape?
Answer 1 year ago
Hi John, it is the polyimide film used as the base material of Kapton tape that gets turned into graphene when hit with the laser.
Question 1 year ago
I know graphene is a conductor, how could this process be used to make semi-conductor?