Introduction: Dominos Pizza Elevator ( Contactless Delivery )
* Dominos didn't pay me to make this, I just like their pizza! *
As part of Mark Rober's Creative Engineering course on Monthly, I was tasked with creating a project that didn't use electronics / microcontrollers and was related to food.
I can't remember the last time I worked on a mechanical-only project, so it was a good challenge! After thinking about different scenes and interactions related to food, I decided to play off "Contactless-Delivery" with a Pizza Elevator.
The design went through a couple of revisions, as the actual raising/lowering mechanism was simplified.
Though the final project worked, if you're going to make this yourself, there are a couple of changes I'd make to help your make go smoother! I'm working on an updated version with a lot more bells and whistles. If you're interested, check back for that in a couple of weeks!
Supplies
Materials
- Birch Plywood ( 0.686" in my case )
- 3mm Birch Plywood
- #216 Screw Eyes
- Some kind of thin strong twine
- A couple of washers
- 0.5" Oak Dowel
- Wood Glue
- Paint
Tools
- Wood CNC
- Laser Cutter
- Drill Press / Hand Drill
- Sandpaper
- Wood Saws
- Lots of clamps
- Paintbrush(es)
Step 1: Design & Prototyping
I started out with a sketch over a picture of the balcony from Google Maps.
Then I went through and defined the requirements for the final build. These included ease-of-use elements like a crank to raise/lower the platform and that constraint that the final design is able to be removed/reattached easily.
Originally, I was planning to use aluminum square tube for the frame and had built the first design around GT2 belts and pulleys. The idea was to have axels and belts running through the tubes to spools in each of the four corners of the platform.
Some revisions later, and after looking at the tools available to me, I switched to using CNC'd plywood. I was worried about getting the gearing and axels to work correctly and got some advice from peers that the mechanism was overly complicated.
Taking some inspiration from sewing machines, I decided instead to have a central spool where each line is threaded to. These lines run through metal eye screws and connect to the corners of the platform.
This design greatly simplified manufacturing and construction so I moved forward with a laser-cut cardboard prototype to test it out. Using a tin can as the spool and a pencil as the axel, I was able to reliably raise and lower the platform. That is until the pencil snapped... good to know that's a weak point for the real build.
That proved the core function and was enough for me to move onto the final build. In retrospect, I should have tested that mechanism AND how it functioned at increasing payload weights. The string glid smoothly on the eyescrews with no weight but started to bind a bit as the payload weight increased.
Step 2: Wood Build
I spent more time than I'd like to admit setting up the CNC file. I'm a volunteer Maker (Maketeer) at the Seattle Makers (SM) Makerspace, and had just completed my training on their Shapeoko CNC the night before. I made the original model in Autodesk Fusion 360 then exported the sketch outlines as DXF's. I imported the shapes into VCarve Pro ( The G-code generator of choice for SM ), and set up the files. Instead of modeling the string channels, I drew the paths directly where I wanted the strings to go and had VCarve cut along the center of them.
I wanted the actual elevator platform to be as light as possible so I cut out a cross pattern in the wood. To save time, and avoid a long pocket operation, I had it cut all the way through. To make the top solid again, I did a 3mm pocket on the top and laser-cut an insert to glue in that place. In the same process, I also cut an additional ring for the spool and some ( later unused ) ratchet gears. I'm planning to actually utilize the gears in a subsequent build, ensuring the loaded elevator platform can't plummet back down.
The CNC cut completed in just around 2.5hrs, and after cutting off tabs and sanding down the files, I was ready for assembly.
The eye screws were screwed into sections of the dowel so I could thread them easily and then slot them into their place along the track. ( Detailed in the painted picture above )
Everything was glued together with wood glue, interlocking pieces were sanded until there was a snug fit. The spool slices were all glued together and then glued to the axel. The strings were cut to length, threaded through the eyescrews and screwed into their slots on the spool.
Step 3: Paint & Test
I painted after assembly was completed... which wasn't the best idea. For next time, I'd absolutely paint before... I think I was just too eager to see if the mechanism worked right!
That said, I was really happy with the finish. To get the right color, I color matched Domino's colors off of a gift card at Home Depot.
With the whole thing assembled and looking nice, we ran a test lowering and raising a couple of textbooks around double the weight of the pizzas I'd be actually elevating.
When that worked, all that was left was to set up delivery from Dominos and hope everything went to plan!
The delivery-person was great and knew exactly what to do when I lowered the platform. If you look close at the video, you'll see a piece retaining one end of the spool popped out, right as the pizza reached the balcony. Not a catastrophic failure though, and the pizzas arrived safely.
I shared the video on Reddit and some delivery drivers were quick to recommend upgrades. Maybe for v2? :)
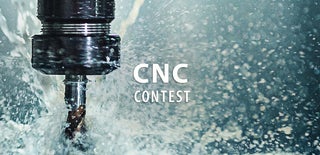
Participated in the
CNC Contest
Comments