Introduction: Milk Jug Vacuum Forming - Recycled HPDE Plastic
This Instructables shows you how to reclaim / re-use / re-cycle HDPE plastic, from waste milk jugs - and use them for Vacuum Forming. It saves using virgin plastic, (say for prototyping), is food safe, is flexible once moulded (good for concrete mini moulds), and does not give off harmful fumes upon careful heating (Easter Eggs Treasure!).
(Please consider voting in Trash to Treasure contest, if you liked it! Thanks.)
You may have access to an industrial grade Vacuum Former in your workshop or maker space, but if you are using a hobby Vac Former, like a Mayku*, you do need to avoid draughts to keep the plastic extra warm. I made a heat shroud here (LINK to Instructable) to Fix It...so do take inspiration from it if it helps with thicker HPDE containers, etc. (though at your own risk).
This I'ble is not trying to be preachy, and I'd be the first to admit that this is hardly gonna save the planet, but I think it provokes some worthwhile discussions about what materials and resources are perhaps 'good enough' for a prototype - and are right under our noses!?
This mould in HDPE is probably 80% as good as one in virgin plastic, (perhaps more??), and it costs essentially nothing, as I was going to buy milk anyway (it's even better value in bulk). When it is used, it can still be put in the same recycling bin it was intended to go, but has performed a useful service on the interim!
Please vote if you liked it, and do share any thoughts on other 'quick wins' around the workshop that play a small part in being more conservative of world resources. Thanks!
Supplies
Vac Former: Mayku Formbox ( *FYI: Mine was a freebie, so please note #ad ) https://amzn.to/3cXVSLG
Milk Jugs. I used the 6pint size ones. It's almost possible with 4 pint, but requires more stretching with the heat gun!
Heat Gun, (LINK) or even a Hairdryer will do on a hot setting. Do wear gloves if it gets too hot to handle.
Scissors.
Bench Vice (not shown).
Small stick of wood is handy to check softening of plastic.
Wooden Moulds (Make whatever you like, just add a small draft angle, wherever possible).
Step 1: Salvaging HDPE From Milk Jug
I took a rough measurement of the vacuum bed size, (which is around 20cm, with a 1.5cm perimeter on the platten). So I figured I needed to extract a 'sheet' about 23-24cm square at least.
As shown, I left excess at the bottom (second pic) and at the top (third pic). These of course 'curl' or 'curve' the form of the plastic, but the heat-gun will soften them out again.
In case you're interested, HPDE is a 'thermoplastic', so can be reheated multiple times with only a little deterioration in its quality, this is why it's also good for recycling. And for you, it'll cope with a few re-heats to try again if not happy with a form.
Step 2: Heat & Stretch (Making the Sheet)
I first did this by hand, and if I'm honest without gloves.
That said, I'd recommend you use some workshop gloves (fabric, not plastic, or even latex), and use a vice as shown to hold one edge as you stretch the overall form. It was in fact easier this way!
As shown the 'bulge' of the milk jug gets 'pulled' into the sheet, with successive working, either through shrinking with heat, or being stretched out.
The first attempt took me a few goes to get right, and avoid over-stretching or tearing the plastics, but after that I was knocking them out in about 2-3mins. No problem!
TIP: Although Milk Jugs were the inspiration, the 5ltr De-Ionised Water jugs were a simpler form, and gave better results, and needed almost no heat gun work at all.
TIP: Hairdryer also works, if no heat gun is available.
Step 3: Preparing the Platten
I checked the spacing of my moulds (really more 'generic' here to test various radii, etc.). I'd personally do an Easter Egg with more time, but this was about validating the concept. Safe to say, sharp angles are hardest, and I put no draft angles to really test the mould.
Step 4: Heating
KEY TIP: I jostled the plastic 'sheet' into the Vac Former. However, I would stress that it is vital to press the 'bump' in the plastic down, away from the heating element above it (see first picture), so as it does not melt onto it. You can even 'heat-gun it down' a little while in the platten.
You will see the HDPE soften and sag down. The peaks will merge and creases will soften out.
The HDPE from the milk jug is relatively thin, so it heats and sags quite fast.
MAYKU TIP: If using the Mayku Vac Former, I suggest using the 'Fix It' Hack I did, to keep the heat from escaping.
Step 5: Vac Formed!
Pulling the HDPE and applying Vacuum to yield the mould!
PRO TIP: If you see any weak-spots in the HDPE, near the edges, you can add some masking tape, which will help stop the tear getting bigger, and allow the vacuum to still be good (i.e. stop any leaks). Another is to keep a rag or tissue near by, and 'plug' any leaks as you see/hear them. (I even saw Adam Savage do this on Tested, so there is no shame in doing this!!).
Step 6: Mould for Free
Although I would not say that the model making industry will forego all sheet plastics to 'save the planet', I do think the use of HDPE for a cheap first prototype or early exploration is fully justified.
Or indeed, if working in say concrete, the 'oily' (polyolefin) plastics make them durable, and will cope with rough casting processes, which say ABS will be less flexible to.
And lastly, the food-safe aspect is really good, for a 'free' material. Get that Chocolate out for Easter!
Step 7: FYI: Creases & Webbing
It's worth knowing that so long as your plastic is well heated, any small 'defects' like the ones shown here, may not actually be a problem. As you can see, it looks 'failed' on the outside, but on the inside of the moulds, the plastic has welded together, and has no defect visible. So don't panic, and carry on!
Step 8: Appendix / Refinements
As mentioned earlier, I found that 6pint milk jugs are abundant, but 5ltr water jugs are best.
Here is a sequence of me testing that. It's about 2-3 times as thick as the milk jug plastic, so the mould is very strong, and I'd even go as far as to say, I'd struggle to complain about this in contrast with virgin material moulds I've done.
Step 9: Thanks! Please Share Any Projects =)
Hope this is useful. If you liked this sort of thing, please consider checking out some of my other work:
https://www.youtube.com/judepullen
http://www.judepullen.com/designmodelling/
And please do vote if you liked it, and share any work you did inspired by this below!
Many thanks,
Jude
PS - Formbox Link here: https://amzn.to/3cXVSLG
Step 10: Update: Biscuit Tin Hack!
Stainless Steel Strapping can be tricky to source. So I found a hack with a biscuit tin (~23cm x 24cm)
So this is even simpler now! And you get to eat biscuits in the name of innovation!
- Gather tools and biscuit tin.
- This was perfect: https://www.tesco.com/groceries/en-GB/products/27...
- Cut the rim of the tin.
- Cut anti-clockwise if you have right handed shears. It's easier.
- Keep the base.
- Scribe the height with a block and pen as shown on the outside....
- ...and the inside.
- Cut
- Note burrs
- Sand off
- Use some scrap for the handles...
- Fold as shown.
- Trim down
- Roll over
- Done!
- Use the base for something else =)
- Oh - and in hindsight - wear gloves. It can be sharp. And if new to this, perhaps wear goggles too!
- Tesco biscuit tin - FYI.
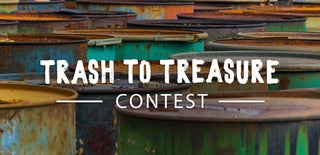
Participated in the
Trash to Treasure Contest
8 Comments
2 years ago
Thanks for this great Instructable! I just made a vacuum forming machine and did my first tests with recycled HDPE jugs. I'm a Design teacher at an international school, and I hope to use this for making props and costumes for an option class that focuses on cosplay.
https://youtu.be/PQNraQ8kSqs
Reply 2 years ago
Thanks for the note - very cool to hear you're trying it out. Do share any photos!
And perhaps drop a hello on Twitter @Jude_Pullen
3 years ago
Cool! Never tried vacuum forming, but I've found your cardboard instructions to be useful in the past. Thanks for putting stuff out there!
Reply 3 years ago
Thanks a lot for the comment. Glad it was useful!
I've been doing more cardboard @Jude_Pullen also FYI.
(Recently a Hot Wheels ramps in card, for example!)
3 years ago on Step 9
Also you could use 2-3litres pop bottles as well for prototypes.
Reply 3 years ago
Have you had any success? I found that PET/PETG has such a high shrinkage that it rips itself out of the platten/frame. Do share any ways to get it to work, as the 2ltr bottles do in fact yield a 25x25cm square!
3 years ago
I do vacuum forming with milk bottles as a kids project using the Make Magazine peanut butter jar vacuum former and a heat gun. https://makezine.com/2010/07/08/toolbox-diy-vacuum-former/ They are always thrilled!
Reply 3 years ago
This is awesome! I clicked round back to the I'ble. It's 2007! WOT. It's like you were waaaaay back in the day. Amazing =D
I'd not thought of doing mini cars, but pretty cool to have upscaled to larger objects with this. Do post if you fancy revisiting it!